Just a few months ago, I decided to get back to boolit casting and bought an off brand two burner camp stove. A cast Iron skillet pulled lead melting duties, and a small decorative cast iron skillet attached to vice grips was used as a ladle.
I bought a bucket of wheelweights from a local tire shop for $20 and began sorting the wheelweights.
After reading a lot about zinc wheelweights on castboolits.gunloads.com I started sorting the wheelweights a little at a time. I did it at work when I had nothing better to do, I sorted them at home, and little by little I got them sorted.
And much to my surprise, I ended up with less than a 1 lb coffee can full of zinc and iron wheel weights.
I got about 80 lbs of clip on wheelweights, and 25 pounds of stick on wheel weights.
I thought I got a decent deal at around .20 cents per lb.
After getting them all sorted, I began melting the lead and casting them into ingots. I used a large muffin pan from wal mart as an ingot mould, and these ingots are slightly more than 2 lbs a piece.
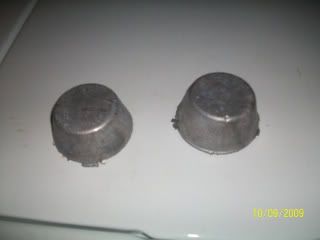
Once my new Lee mould arrived, a 125 gr round nose boolit of .356” diameter, I started casting boolits.
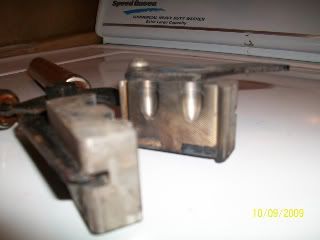
Well, I fluxed with wax from another scented candle (also pilfered from the wife, she caught me this time) and poured with a ladle.
I was getting rounded bases on my boolits, and couldn't figure out why. After appealing for help, I was informed that it was likely my alloy was too cool.
I tried and tried to get higher heat transfer into my melt, but just couldn't seem to get the temperature high enough to give me good boolit fill out 100% of the time.
So, after once again pleading my case, a member on castboolits suggested I invest in a Lee melter.
I did some research and ordered a new Lee Pro 4-20 pot. (I cringe at that designation every time I read it) The pot came rather quickly from Midway USA, and cost me $70 after shipping.
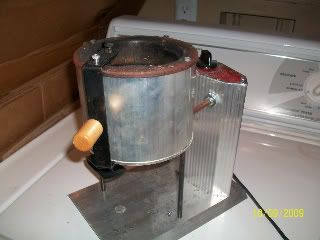
The pot has bottom pour capability, which is really good as my ladle is too large to fit in the pot.
I quickly pilfered a spoon from the kitchen (wife doesn't know, we have lots of spoons) and attached it to the vice grips.
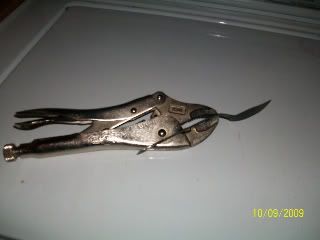
Works quite well for fluxing and skimming purposes. I set the pot to high and it quickly melted my lead, so quickly that I was thoroughly surprised.
And I was able to get mould fill out much more often. But everything was not fixed. I was still getting what I felt to be a high reject rate due to improper fill out.
Once again, I brought my issues to castboolits, and was advised that Lee moulds tend to suffer from poor venting. So to improve this, I took a sharp knife to the aluminum mould blocks, and traced over the vent lines to just noticeably open them up.
Then I loosened the sprue plate just enough to allow it so swing open using it's own weight.
Viola! I now able to cast perfect boolits 90% of the time.
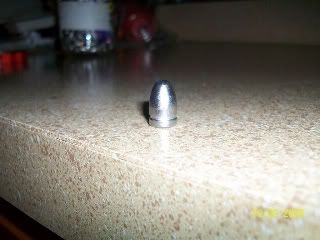
Now, after casting 1000 of these little boolits, I decided it was time to figure out how I was going to lube them.
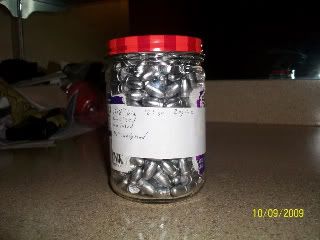
Lee Liquid Alox was suggested, but is about the consistency of mule snot, and tends to remain sticky for quite a while after application.
Well, a member by the name of geargnasher on castboolits suggested a mix of Liquid Alox, Johnson's paste Wax, and Mineral Spirits.
After a small misunderstanding, he agreed to send me a small sample. These guys are great. They want each other to be successful.
I received the sample, a couple of boolits lubed with the mix, and instructions on how to use it.
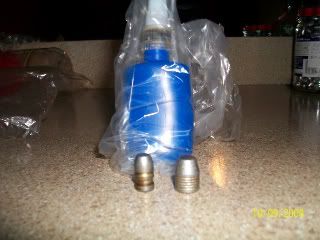
Well, I tried some and am quite impressed, all you do is place the boolits and some of the lube in a ziploc bag, and massage them around, then pour them on wax paper and dry them.
The result was a light coat of brown on the boolits with a barely perceptible stickiness, which may have had something to do with the humidity around here.
So now I am waiting on a Lee Semi Wad Cutter mold for my .38 spcl and still don't have the tools to load completed rounds.
So we will see how that goes when I get the equipment, until then I'm just enjoying creating these little lead things.
This comment has been removed by the author.
ReplyDeleteCongratulations on your successful casting. One thing I did wrong when at your stage was to cast about 1000 boolits, lube them all, and load 500 of them, only to find that I needed to size them to .358. Using them 'as cast' was leading my barrel quit a bit. Some folks are lucky and can use "as cast" without leading. You may want to load up 100 and see how it goes before loading more than that.
ReplyDeleteRandy